Environment is the center of attention for consumers, who demand products with a low environmental impact, and for companies, that adopt more and more eco-friendly strategies. In the food & beverage industry the challenge companies are facing involves two aspects: the first one refers to the production processes that are reviewed to be as eco-friendly as possible and the second one is the use of captivating, eco-friendly and recyclable packaging.
In SMI, environment and sustainability are combined with innovation. The increasing attention to the market needs requires the development of technical solutions of the latest generation that help boost continuous change and take into account typical elements of the companies operating in the context of the circular economy: cost reduction, energy saving, increasing competitiveness and improvement of the market positioning.
The solution for bottling includes different models of ECOBLOC® ERGON integrated systems for manufacturing, filling and capping of PET and rPET bottles, while the end of line solution includes a wide range of fully automated secondary and tertiary packaging machines.
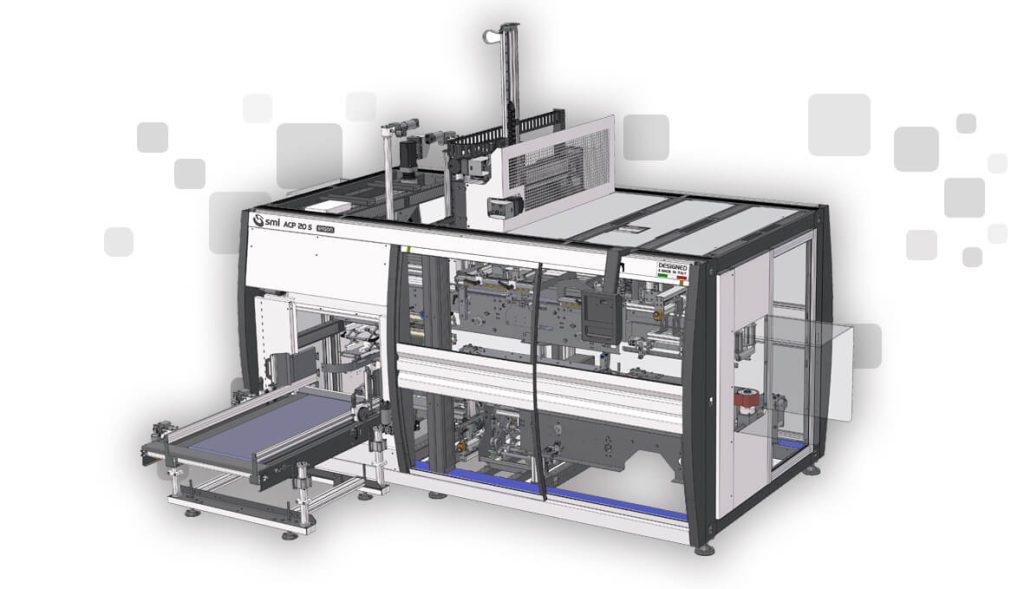
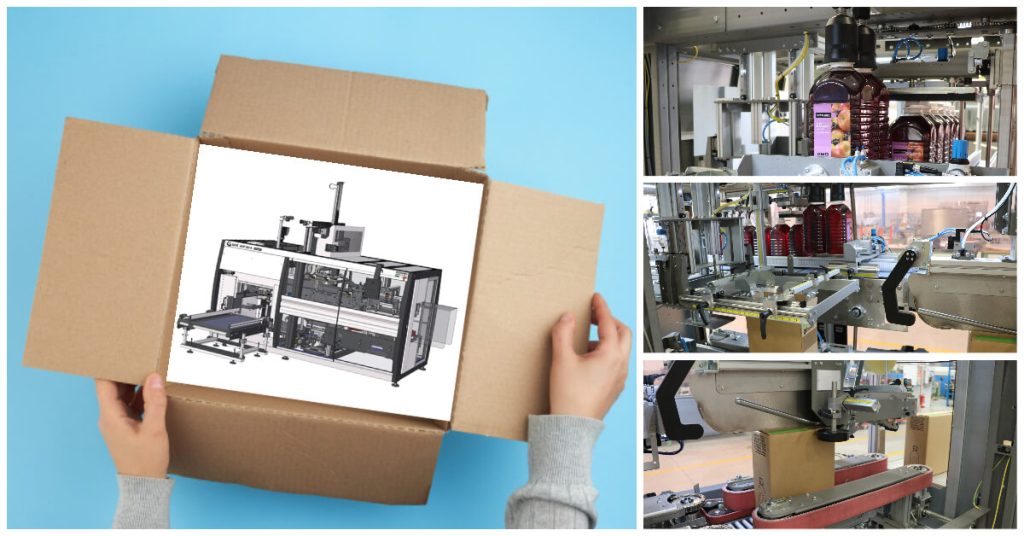
Innovation, reliability and sustainability
The ECOBLOC® K ERGON integrated system is a compact, efficient and eco-friendly solution for manufacturing, filling and capping PET and r-PET (recycled PET) containers.
Recent studies have shown the benefits of the use of plastic bottles, since this solution is unbreakable, safe, with great barrier properties, light and especially recyclable.
Compared to other packaging materials, such as glass or aluminum, PET has a good environmental profile, mainly thanks to its lightness that results in less material produced, less waste, less energy to manufacture it and less fuel to transport packed goods. Thanks to its recyclability and its great capacity/weight ratio, many manufacturers of mineral water and soft drinks have promoted and reevaluated PET and r-PET as convenient and “win-win” solutions in terms of environmental sustainability.
Another strategy that helps safeguard the environment is based on the study of even lighter PET containers that allow to considerably save on plastics and that therefore fully comply with the environmental policy of the largest beverage producers.
End of line connected to the market
SMI offers cutting-edge solutions for the secondary and tertiary packaging industry that are inspired by the concepts of Industry 4.0 and Internet of Things (IoT) and that are even more efficient, flexible, eco-friendly, ergonomic, easy to use and control. The manufacturers of beverages, food, detergents and chemical and pharmaceutical products need to be increasingly competitive to face a demanding market that is constantly changing.
From today you can choose between a wrap-around box and an “American” cardboard box (RSC); in fact, the most recent investments in R&D made by SMI in the secondary packaging in cardboard boxes have led to the birth of the new range of case packers, called ACP (American Carton Packer) suitable for American cardboard case (RSC) with a “pick & place” system for inserting the bulk product into the package.
Choosing between the wrap-around box or the American cardboard box, as well as choosing between a completely closed box or an open tray, remains a subjective aspect of each SMI customer, largely dependent on a series of other factors closely related to the product to be packaged, the commercial strategies of the manufacturing company, logistics and distribution needs, etc.
Packaging in wrap-around boxes or in American cardboard boxes, depends on crucial aspects of the production activity such as material, weight and shape of the container, palletising schemes, speed of the production line. But it also depends on a series of other factors such as the company’s marketing objectives, the budget available, the way consumers buy (whole package or single products), the need or not to display the package on the shelves at the retail point, etc.
The main characteristics of the new case packers are:
• alternate packaging process (stop & go) through the “pick & place” system, capable of making packages at the maximum speed of 20 packs per minute (depending on the format)
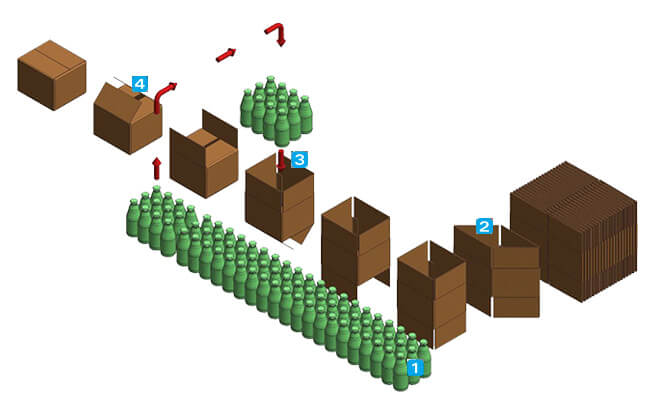
• grouping of products in an alternating cycle, through a pneumatic separation system
• carton magazine located next to the machine, with easy and ergonomic pre-folded punch loading
• packaging in “American” style cardboard boxes (RSC) with loading of the loose product from above
• possibility of overlapping the product in the box during its insertion
• possibility of packaging multiple types of products, such as bags of pasta, rice, coffee, as well as oval containers (such as shampoo) and briks (tea, juice, etc.), simply by changing the gripper
• possibility of processing delicate products, such as wines, sparkling wines and liqueurs, without damaging the labels during processing in the machine
• easy machine access
• reduced mechanical wear and maintenance
• MotorNet System® automation and control technology based on Sercos fieldbus
• depending on the model chosen, the box is closed by means of adhesive tape or hot glue. The model with glue pack closure is equipped with a lower glue unit and a double spray upper glue unit which ensures excellent pack sealing. At the machine outfeed, special lateral upper flap-bends operated by a semi-rotary cylinder keep the walls of the newly made box, pressed.